How Professional Product Packaging Maker Fixing Provider Lessen Downtime and Boost Performance
In today's competitive landscape, the efficiency of packaging operations is paramount for preserving a successful business. Professional product packaging device fixing solutions are vital in minimizing downtime and improving productivity through specialized diagnostics and prompt treatments. By applying preventative maintenance methods, these services not just avoid costly failures yet additionally guarantee constant item high quality and process. The effects of such solutions expand past immediate repair work-- unpacking the wider effect on functional effectiveness reveals vital understandings into long-term productivity techniques (packaging machine repair service). The concern continues to be: exactly how can services utilize these solutions to attain sustainable growth?

Importance of Timely Fixes
Timely repairs of product packaging devices are vital for preserving operational efficiency in any manufacturing atmosphere. When machinery breakdowns or breaks down, it can result in significant disturbances in production lines, resulting in increased downtime and shed income. The longer a product packaging maker remains out of payment, the higher the effect on general performance, potentially causing delays in satisfying orders and diminishing consumer satisfaction.
In enhancement to the instant economic implications, delayed repair services can result in a lot more considerable damages to the machinery. Parts that are not addressed quickly can weaken better, requiring even more expensive repairs or total replacements, which might have been stayed clear of via timely intervention. Normal maintenance and timely fixings can enhance the life expectancy of packaging equipments, ensuring that they operate at ideal performance degrees.
Purchasing specialist product packaging device repair service solutions is essential for reducing these dangers. An aggressive approach to repairs not only keeps manufacturing schedules but also fosters a culture of dependability within the organization. By prioritizing prompt repair work, companies can preserve their one-upmanship, optimize resource allocation, and ultimately improve their profits via boosted operational performance.
Knowledge in Diagnostics
When it concerns maintaining the efficiency of product packaging machines, proficiency in diagnostics plays a pivotal role in recognizing issues prior to they rise into significant failings. Experienced technicians make use of advanced analysis devices and techniques to perform complete evaluations of machine efficiency. This proactive method allows them to identify the root triggers of malfunctions, whether they stem from mechanical wear, electric mistakes, or software disparities.
Efficient diagnostics not only promote quick identification of problems yet likewise improve the overall integrity of packaging procedures. By conducting comprehensive analyses, service technicians can examine the wellness of crucial parts, guaranteeing that also minor abnormalities are attended to promptly. This attention to detail lessens the threat of unforeseen malfunctions, which can result in pricey downtime.
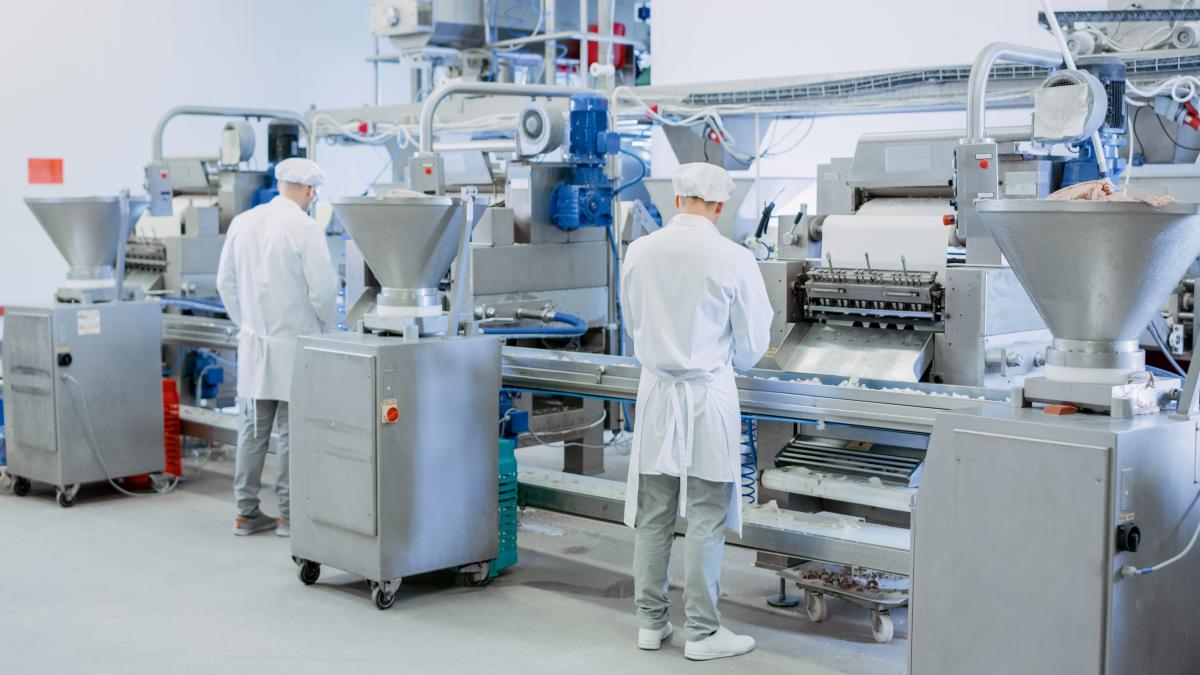
Preventive Maintenance Benefits
Preventive maintenance complements specialist diagnostics by proactively resolving possible concerns prior to they manifest into severe issues. By carrying out a structured preventive maintenance program, business can substantially minimize the threat of unforeseen device failures, thereby decreasing expensive downtime. Regular inspections, cleaning, and parts substitute assistance guarantee that product packaging equipment runs at optimum performance.

Furthermore, preventive maintenance adds to enhanced safety and security problems within the work environment. By identifying and fixing potential threats before they escalate, organizations develop a safer atmosphere for their workers. This aggressive method not just shields employees but likewise cultivates a society of obligation and caution.
Last but not least, consistent precautionary upkeep can enhance item top quality. Well-maintained devices runs a lot more continually, decreasing the probability of flaws and guaranteeing that product packaging fulfills rigorous industry standards. In recap, preventive maintenance is an important approach for optimizing performance and ensuring operational excellence.
Custom-made Service Solutions
Acknowledging the one-of-a-kind demands of each business, customized solution remedies for product packaging equipment repair deal customized strategies that enhance operational efficiency. These remedies are developed to attend to details challenges encountered by different industries, ensuring that machine downtime is minimized and performance is maximized.
Professional fixing solutions start with an extensive assessment of a company's product packaging procedures. By recognizing the specific equipment entailed and the demands of the production atmosphere, professionals can establish a customized repair and maintenance strategy. packaging machine repair service. This may consist of specialized training for in-house staff, the execution of anticipating maintenance modern technologies, or the arrangement of dedicated assistance throughout optimal manufacturing times
Furthermore, customized options can integrate versatile service arrangements that line up with a firm's functional timetable, permitting repair work to be executed during off-peak hours. By focusing on the unique demands of each business, these custom solutions make sure my sources that fixings are not only reliable but likewise effortlessly integrate right into existing workflows.
Inevitably, the concentrate on modification makes it possible for business to maximize their packaging processes, causing improved integrity and performance of machinery, which is essential for keeping competitive advantage in today's busy market.
Effect On Overall Performance
Custom-made service options not just address details repair work needs however additionally play a substantial role in enhancing total operational efficiency. By supplying targeted treatments, professional product packaging machine repair work services straight lower the check out here frequency and period of tools failings. This aggressive technique ensures that assembly line stay functional, minimizing disturbances that can bring about costly downtime.
Moreover, efficient repair solutions add to smoother process, as well-kept equipment operates at ideal efficiency degrees. When makers work properly, the quality of packaged items enhances, resulting in fewer problems and much less rework. This enhancement not just enhances performance yet additionally strengthens customer complete satisfaction.
On top of that, regular upkeep and quick response times from repair professionals cultivate a culture of integrity within the company. Workers can focus on their primary tasks as opposed to bothering with prospective equipment failures. The general throughput of the production procedure increases, allowing firms to satisfy demand extra effectively.
Eventually, the strategic financial investment in expert repair solutions converts to improved performance across all functional aspects, making sure that companies can adjust and flourish in an open market. This synergy between maintenance and productivity is crucial for long-lasting success.
Verdict
Finally, specialist packaging maker repair services play an important role in decreasing downtime and enhancing efficiency within manufacturing settings. Prompt repairs, professional diagnostics, and preventative maintenance add to the reliability of devices, while personalized solution solutions attend to particular operational requirements. The collective effect of these services leads to improved general performance, enabling companies to keep manufacturing timetables, copyright product high quality, and properly satisfy market needs - packaging machine repair service. Purchasing such solutions ultimately drives sustained functional success.
Comments on “Prevent equipment failures with a dependable packaging machine repair service.”